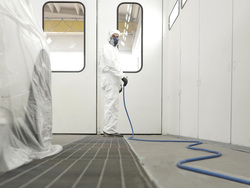
Spesso sottovalutato per gli utilizzi in carrozzeria, il tubo dell’aria compressa svolge in realtà un ruolo fondamentale. Per questo Zeca ha deciso di studiarne uno specifico per le applicazioni sia in forno sia in preparazione. Il suo nome è Flex.
Nelle lavorazioni di carrozzeria non è la prima cosa a cui si pensa, eppure il tubo dell’aria compressa può rappresentare una criticità. Spesso considerato un elemento naturale e necessario per qualsiasi lavorazione, dalla levigatura alla verniciatura, al tubo si presta davvero attenzione solo quando rappresenta un problema, come ad esempio il disordine o un impiccio sul pavimento, oppure quando è la causa di vere e proprie perdite di tempo dovute dall’attorcigliamento o al contatto con superfici appena trattate.
Insomma, del tubo dell’aria compressa non ci si preoccupa finché non diventa un problema.
Tendenzialmente, infatti, il tubo dell’aria compressa è un accessorio che si ricompra regolarmente ogni tot di mesi ed è di tipo standard: lo stesso utilizzato nell’officina meccanica e in generale per ogni applicazione ad aria compressa.
Ma è davvero così? La carrozzeria ha esigenze differenti dal resto del mercato? Per capirlo, Zeca - azienda produttrice di avvolgitori e di una vasta gamma di attrezzature per l’autoriparazione - ha deciso di indagare meglio la questione parlando con i diretti interessati.
Il “Tubo Tour” e i risultati dell’indagine
Il punto era capire se i carrozzieri avessero necessità particolari e analizzare il lavoro direttamente in carrozzeria per capire quali potessero essere anche le criticità nascoste.Per questo l’azienda ha realizzato lo scorso anno un roadtrip di oltre 6.000 km che ha toccato praticamente tutta la penisola e ha permesso a Zeca di analizzare le situazioni più disparate.
Dopo due mesi, in cui sono stati intervistati oltre 200 tra carrozzieri e rivenditori, i risultati hanno permesso ai tecnici di avere una serie di indicazioni che sono poi servite a realizzare questa nuova applicazione.
Vediamo innanzitutto quali sono i fattori che creano problemi ai tubi nelle applicazioni in carrozzeria.
Il primo aspetto che tutti i carrozzieri hanno segnalato è il peso del tubo e la sua rigidità. Se infatti nell’utilizzo di attrezzature pesanti, come una levigatrice o una pistola a impulsi, il peso del tubo è trascurabile rispetto a quello dell’utensile, in cabina di verniciatura il peso diventa un fattore fondamentale: ogni grammo in meno permette una maggiore precisione nella verniciatura, così come la rigidità del tubo stesso, che se non è sufficientemente flessibile limita la libertà di movimento della mano.
Ma il vero nemico dei tubi per l’aria compressa, soprattutto nelle zone dove si spruzza, è rappresentato dai depositi degli aerosol di verniciatura. Con il tempo, infatti, i depositi di vernice si stratificano sul tubo, rendendolo via via sempre più rigido e meno performante.
Infine, nonostante le temperature dei forni moderni non siano più proibitive come quelle di un tempo, sicuramente la resistenza alle alte temperature resta un fattore discriminante.
Una soluzione specifica per i carrozzieri
Ecco quindi che l’azienda ha dato il via a un processo di ricerca e sviluppo, che tenendo in considerazione questi elementi, l’ha portata a realizzare un tubo specifico per le applicazioni in carrozzeria. Uno sviluppo congiunto che ha visto partecipare più aziende, nel processo che va dalla mescola della gomma alla treccia interna fino ai trattamenti superficiali del tubo.Vediamo allora perché questo “semplice” tubo, il cui nome è Flex, rappresenta in realtà un utile strumento di lavoro in carrozzeria e un alleato nelle lavorazioni.
In primo luogo, il tubo resiste a temperature di 60° C senza problemi anche per periodi prolungati. La composizione stessa del tubo stesso è differente da quella dei prodotti tradizionali. Si tratta, infatti, di un tubo a doppio strato, che invece della classica maglia di rinforzo ne utilizza una specifica in materiale sintetico, che permette di avere due vantaggi: da una parte una notevole riduzione di peso, dall’altra limita il formarsi di volte nel tubo.
Nonostante sia concepito specificatamente per i lavori in cabina di verniciatura, dove difficilmente si utilizzano pressioni molto alte nel circuito dell’aria compressa, il tubo consente di lavorare con pressioni fino a 15 bar, risultando così utile anche per le lavorazioni di preparazione.
L’ultimo punto, relativo al deposito degli aerosol, ha rappresentato la sfida più grande per la superficie esterna. Oltre a essere liscia e non appiccicosa (caratteristiche che spesso hanno tutti i tubi nuovi), la copertura esterna doveva essere anche antistatica. Sono infatti proprio le cariche superficiali a favorire l’aderenza del pulviscolo sul tubo. Più facile a dirsi che a farsi, perché l’antistaticità della gomma si ottiene solo additivando la mescola stessa con prodotti che la rendano tale. Il problema è che questi additivi hanno spesso un’alta componente volatile, che fa quindi perdere l’effetto antistatico alla gomma con il passare del tempo.
Zeca ha quindi individuato un additivo poco volatile che, secondo le previsioni dell’azienda dovrebbe garantire l’antistaticità per tutta la vita utile del tubo.
In sintesi, il risultato di questa ricerca è Flex, un tubo silicon-free composto da un sottostrato ad alta tenacità, che garantisce la massima resistenza meccanica; una maglia di rinforzo che riduce al minimo l’effetto memoria e rende il tubo ultraflessibile anche con raggi di curvatura ridotti; una copertura antistatica che protegge il tubo dalle polveri e assicura una lunga durata nel tempo.